ANODE
A sacrificial anode is a part of a cathodic protection system and is attached to a steel structure to protect it against corrosion. Cathodic protection works by placing a Anode or Anodes which acts as a External device in an electrolyte to generate a circuit as result current flows from the anode through the electrolyte to the surface of the structure. Corrosion moves to the anode to stop further corrosion of the structure like Tower, ship, oilrig etc. Our professionals ensure specifications that the manufacturing process is carried out under the industry norms. Our team offers our outstanding products at cost-effective rates. We are offering a one-stop solution to ensure products as per industry standards. |

Popular Material Types for Anodes as per Environment :
- Zinc for Sea Water,
- Aluminum for Brackish Water,
- Magnesium for Fresh Water,
Popular Types of Anodes as per Fixation :
- Bolt On Anodes – (Zinc, Magnesium & Aluminum),
- Weld On Anodes – (Zinc, Magnesium & Aluminum),
- Tank Anodes – (Zinc & Aluminum),
- Pencil Anodes – (Zinc),
- Anodes with Backing Sheets,
Sacrificial anodes are cast as per basic geometric shapes:
- Long, slender, Stand Off type;
- Flat-plate,
- Flush mounted type;
- Bracelet type.
Application
Sacrificial anodes are used to protect the structures –
- Fuel (Oil & Gas) pipelines – Upstream, Midstream, Downstream and Offshore,
- Water & Waste Water Systems
- Petrochemical
- Marine – Ship and Boat hulls, Offshore oil platforms,
- Onshore oil well rigs,
- Cell Towers,
- Metal reinforcement bars in concrete buildings and structures.
Types of Anodes
1) Galvanic anode protection systems working –
A Galvanic anode protection system works by utilizing sacrificial anodes connected to a protected structure in a circuit. Galvanic anodes use the natural voltage differential or potential, between the anode (more negative) and the structure (less negative) to drive current off the anode and to the structure.
The anode which is normally made from metal such as zinc, is connected to the reinforcing steel and the potential difference between the zinc and the steel causes a small protection current to flow from the zinc to the steel.
Galvanic anode protection consists of applying a protective zinc coating to the steel to prevent rusting. The zinc corrodes in place of the encapsulated steel. These systems have limited life spans. The sacrificial anode protecting the underlying metal will continue to degrade over time. Until the sacrificial anode is no longer capable of supplying protection.
2) Impressed current cathodic protection working –
Impressed current anodes use an external power supply (a perpetual source of electrical flow) to drive current off the anode and to the structure.
This sacrificial anodic method of protection uses a metal more active than the base metal to “sacrifice” ions. These “sacrificial anodes” (usual alloys such as magnesium, aluminum, or zinc) have a stronger electrochemical potential. This method can often provide much longer protection. The anode is supplied by an unlimited power source.
This type of system is typically used when galvanic systems are not sufficient to Prevent corrosion. In an impressed current system, there is an active DC power Source (Rectifier that forces current out of a buried or submerged anode), which allows more current to flow to the metal structure. In a way, this provides a continuous protection from corrosion and a most effective corrosion prevention methods and is exceptionally long lasting.
Driving voltage for this system are adjustable, depending on the local soils and the life remaining in the anode. The required current output can vary significantly with the installation. With some installations such as Uncoated seawall pilings requiring hundreds of amps, Impressed systems are best suited for high-resistivity soils and high-current requirement system.
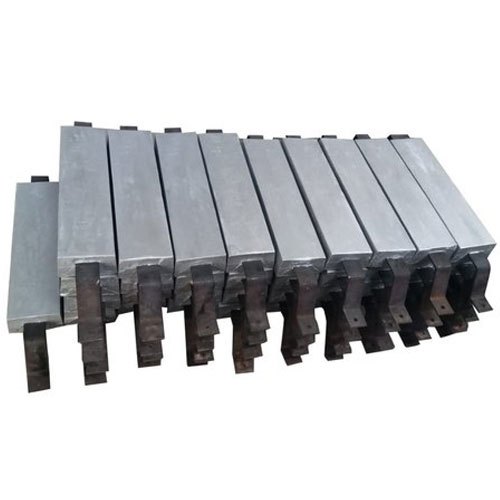
Aluminium Anodes
Country of Origin: India
Certification: ISO 9001:2008 Certified
Color: White
Form: Solid
Closed Circuit Potential: 1.07 V
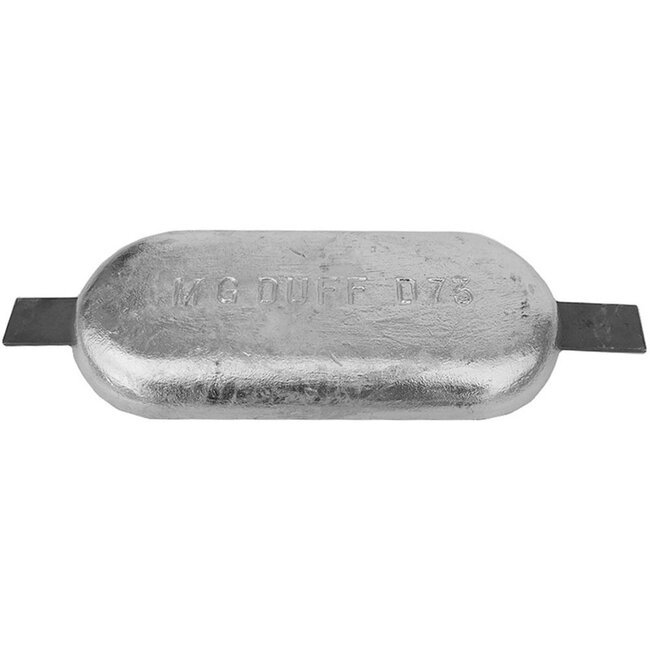
Zinc Anodes
Usage/Application: Ship
Color: Grey
Shape: Rectangular
Surface Treatment: Powder Coated

Sacrificial Aluminum Zinc Anodes
Material: Aluminium
Usage/Application: Ship Repair,Sea platform,offshore
Color: Grey
Surface Treatment: Powder Coated
Thickness: 25mm
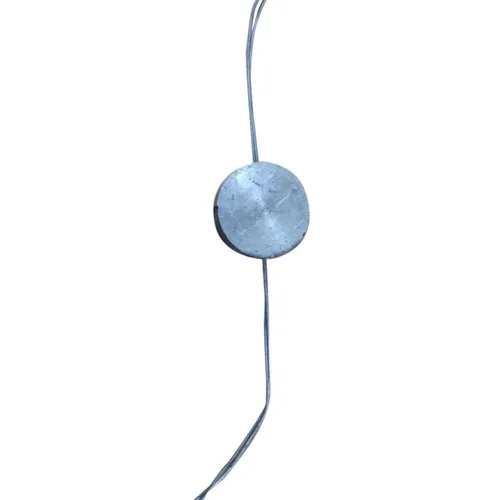
Concrete Zinc Anode
Usage/Application: Concrete Repair
Color: Grey
Surface Treatment: Powder Coated
Thickness: 25mm
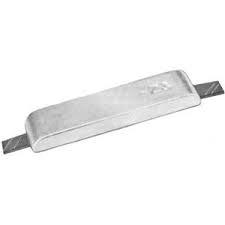
Zinc Hull Anode
Usage/Application: Ship
Color: Grey
Thickness: 40mm
Made in: India
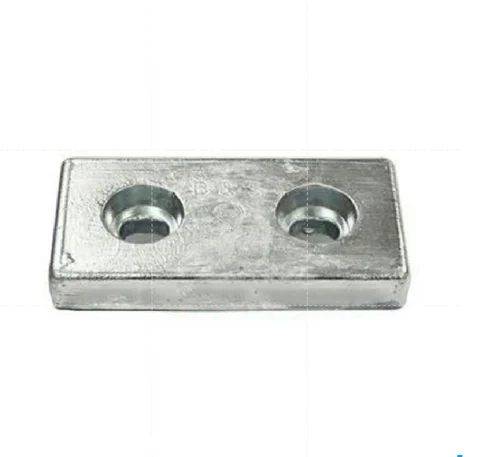
Zinc Bolted Anode
Material: Zinc
Color: Grey
Surface Treatment: Powder Coated
Thickness: 25mm
Made in: India
Main Technical Parameters of MMO Tubular Anode
CHARACTERISTICS | DESCRIPTION |
Substrate | Titanium Gr1 |
Coating | Iridium Oxide (IrO2), Ruthenium Oxide (RuO2), Tantalum Oxide (Ta2O5) |
Shape | Tubular |
Length | 50-1500mm |
Diameter | 16,19,25,32mm |
Wall thickness | 1, 1.5, 2mm |
Application | Deep Well, Storage Tank |
Environment | Brackish Water, Fresh Water, Seawater, Shallow Vertical Ground bed, Soil |
Design Life | Specified 20-100 years |
Our professionals ensure specifications that the manufacturing process is carried out under the industry norms. Our team offers our outstanding products at cost-effective rates. We are offering a one-stop solution to ensure products as per industry standards. We are equipped with advanced and latest machinery for providing the best quality products to the customers. We provide our products to the customers to achieve their maximum satisfaction and offer quality products at budget-friendly rates.
Contact for Pipe repaire Leak.
For more details on the products contact us.
Half Pipe Sleeve, Half Repair Pipe Sleeve, Pre-Stressed Metallic Sleeve.