Insert Pipe Sleeve
In the pipeline manufacturing sector, goods are often processed, shipped, or sold through long-distance pipelines. These pipelines usually use pipes that measure around 40–45 feet in length. To cover greater distances, individual pipes must be joined together. At this point, selecting a reliable Insert Pipe Sleeve Manufacturer becomes essential.
Most commonly, pipes are joined by welding their ends. However, this method comes with risks. Welding generates high heat, which often burns off the protective polymer coating at the joints. As a result, the bare steel surface gets exposed to corrosion and harsh chemicals flowing through the pipe.
Therefore, to protect the girth weld from such damage, using a pipe sleeve is necessary. It acts as a barrier between the joint and corrosive fluids. Most importantly, choosing a trusted Insert Pipe Sleeve Manufacturer ensures long-lasting protection, improved safety, and greater pipeline reliability.
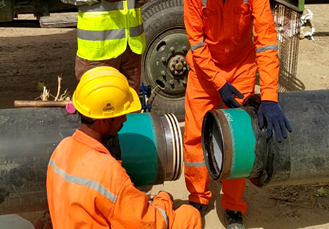
Reliable Protection by Leading Insert Pipe Sleeve Manufacturer
The Insert Pipe Sleeve is an innovative solution designed to prevent damage at exterior field welds, ensuring the integrity of pipelines. Developed to protect the welded portion of the girth from corrosion, it allows for 100% external coated piping even after welding. These sleeves are commonly used for welded tubing and metal fittings, including individually painted components.
As a trusted Insert Pipe Sleeve Manufacturer, we ensure that each sleeve offers a durable protective surface throughout the welding process. This helps maintain the pipe’s polymer coating and eliminates the risk of corrosion at joint areas. Our Insert Pipe Sleeves are available in sizes ranging from 2″ NB to 72″ NB and are compatible with both internal and external coatings using various liquid and powder applications used during pipe processing.
Best Practices by Insert Pipe Sleeve Manufacturer for Safe Installation
To ensure girth weld safety, begin by detaching 1–2 mm from the welding groove and use a burn-back technique to protect the underlying steel substratum. Next, adapt the process to suit the environment by using a container appropriate for corrosive atmospheric conditions. Additionally, improve flow efficiency by designing a smooth top and tapered ends, which help increase flow rate while reducing turbulence. For secure mounting, firmly anchor the fixture by connecting the recessed metal backing ring to the two pipe ends using tabs or pins during the welding process. Finally, you may use any suitable solvent or powder for surface decoration, depending on the desired finish.
SIZE
Reli Sleeve™ can be manufactured for OD & N.B. sizes starting from 2” to 72”.
APPLICATIONS OF INSERT SLEEVES
Many industries rely on Insert Pipe Sleeves for a variety of applications. Below are some of the most common areas where professionals use them effectively.
To begin with, these sleeves protect the internal diameter (I.D.) coating during construction. They actively prevent hazardous weld spatter from damaging the pipe’s interior. Manufacturers design these sleeves to meet industry standards like API 5L, ASME, and ASTM. They work efficiently with both carbon steel and stainless steel, making them suitable for all types and grades of tubing.
Installers appreciate the ease of use. They don’t need specially qualified welders, as standard welding techniques handle the job without any compromise in quality.
Insert Pipe Sleeves also isolate the welded girth section by sealing the internal diameter completely. Once installers place them, the sleeves become a permanent part of the pipeline. They continue to deliver long-term protection against corrosion, just like the carrier tubing.
Engineers and contractors use these sleeves in a wide range of applications. These include gas refineries, desalination systems, jet fuel pipelines, gas injection lines, and firewater systems. They also perform well in petrochemical plants, underwater tunnels, onshore docks, and with various spools and accessories.
SPECIFICATIONS & STANDARDS
- API: American Petroleum Institute
- API 5L – Specification for Line Pipe
- API 1104/ANSI 1331.3 – The procedure and quality of radiography examination limits of acceptability, repair and removal of defects etc.
- ASTM: American Society for Testing Materials Iron and Steel
- ASME Section IX
- SSPC: Steel Structures Painting Council
- SSPC-V1S1 – Visual standard for Abrasive blast cleaned steel
- NACE MR0175 / ISO 15156 – Materials for use in H2S containing Environment in oil and gas production
- NACE SP 0188 – Discontinuity (Holiday) Testing of Protective Coatings
- NACE No. 1 / SSPC-SP5 – White Metal Blasting
- NACE TM 0186 – Holiday Detection of Internal Tubular Coatings of 10-30 Mils Dry Film Thickness
- NACE TM 0384 – Holiday Detection of Internal Tubular Coatings of Less Than 10 Mils Dry Film Thickness
- NACE: National Association of Corrosion Engineers.
MATERIAL USED FOR PIPE SLEEVE
Pipe / Plate
- API 5L PSL 1 & PSL 2 (Gr B to X80)
- ASTM A53 / ASTM A106 / ASTM A333
- ASTM A36 / ASTM A516 Gr 60, Gr 65, Gr 70
- ASTM A671 / ASTM A672 / ASTM A691
- ASTM A312 / ASTM A358
RECOMMENDED INSTALLATION PROCEDURE FOR INSERT SLEEVES
Start by checking the pipe for any damage. Then, wash off all soil, debris, and waste that may hinder operations. If moisture is detected, the heat pipe automatically stops functioning at 60–80 °C.
Measure the inner diameter of the shaft to ensure it’s within tolerance both horizontally and vertically. Ensure the pipe insert sleeve coating doesn’t cause corrosion or defects. Check the quality of sealing bands, heat-resistant tape, and accessories. Mix epoxy mastic as per the manufacturer’s ratio and return it to the pot within the epoxy’s pot life.
Carry out welding at 7–10 inches per minute (175–250 mm), downhill. Leave a 0.5″ to 1″ weep hole to release gases. Use a weaving motion to ensure proper electrode melting.
Let the weld cool below 120 °C before starting intermediate passes. Close the weep hole with the first filler pass. Complete the weld with multiple downhill passes, removing slag between each. Drive the sleeve until the shaft’s bevel end meets the pins. Inject epoxy evenly and join the next primed pipe until pins meet the bevel.
Follow API 1104 or SAE 31.1 standards. Use minimal power for handling and ensure ventilation. Be cautious of toxic fumes from epoxy or coatings—refer to the MSDS. During preheating, keep the pipe temperature below 120 °C. Connect only the pipe ends—never the sleeve tabs or pipe center.
Contact for Pipe repaire Leak.
For more details on the products contact us.
Half Pipe Sleeve, Half Repair Pipe Sleeve, Pre-Stressed Metallic Sleeve.